Pergola & abri rétractable sur mesure
Pergola
Abri de terrasse
Abri de piscine rétractable
Carport
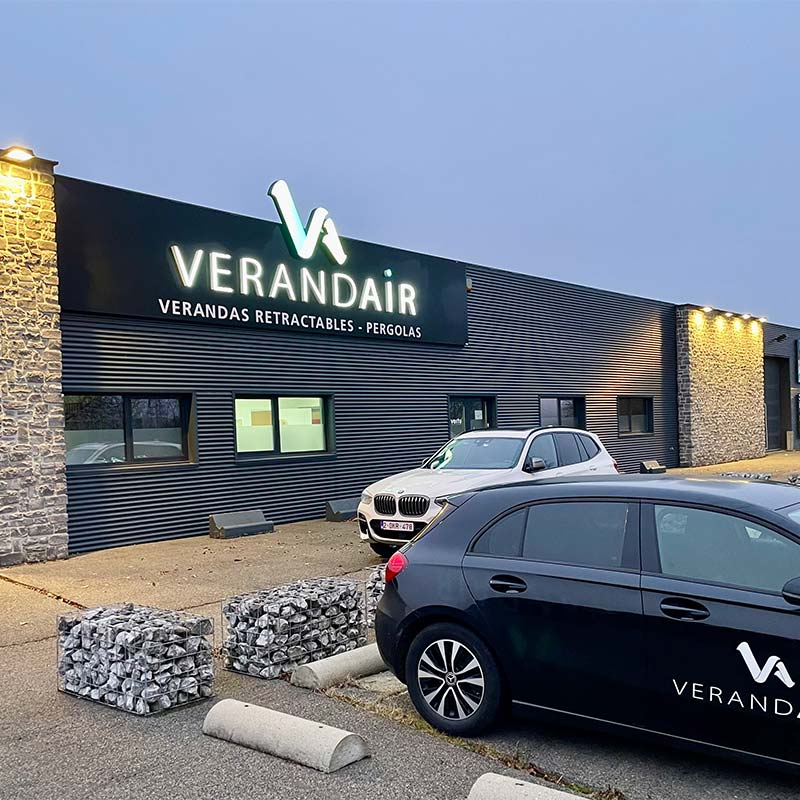
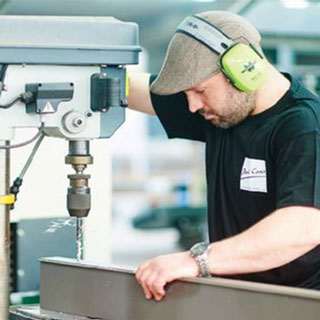
Pourquoi choisir une pergola VERANDAIR® ?
Profitez de votre extérieur toute l’année avec nos pergolas belges de qualité
Verandair est votre fabricant belge de pergolas, abris de terrasse et abris de piscine depuis plus de 30 ans. Nous fabriquons votre pergola sur mesure avec des matériaux 100 % renouvelables. Selon vos besoins et envies, toutes nos pergolas sont personnalisables. Vous bénéficiez d’une installation robuste et fiable, fabriquée, livrée et installée par des professionnels, le tout à un prix abordable !
Êtes-vous prêt à transformer votre extérieur ?
Nos réalisations
Découvrez nos réalisations de pergolas VERANDAIR®
Pergolas fixes, pergolas bioclimatiques, pergolas rétractables, abris de piscine, carport… Consultez nos réalisations, trouvez l’inspiration et démarrez votre projet avec VERANDAIR®.
Nos produits
Trouvez la pergola VERANDAIR® faite pour vous
Abri rétractable, pergola bioclimatique, pergola à toiture fixe, pergola rétractable, abri de piscine, véranda pour Horeca… Chez VERANDAIR®, nous avons un modèle adapté à vos besoins.
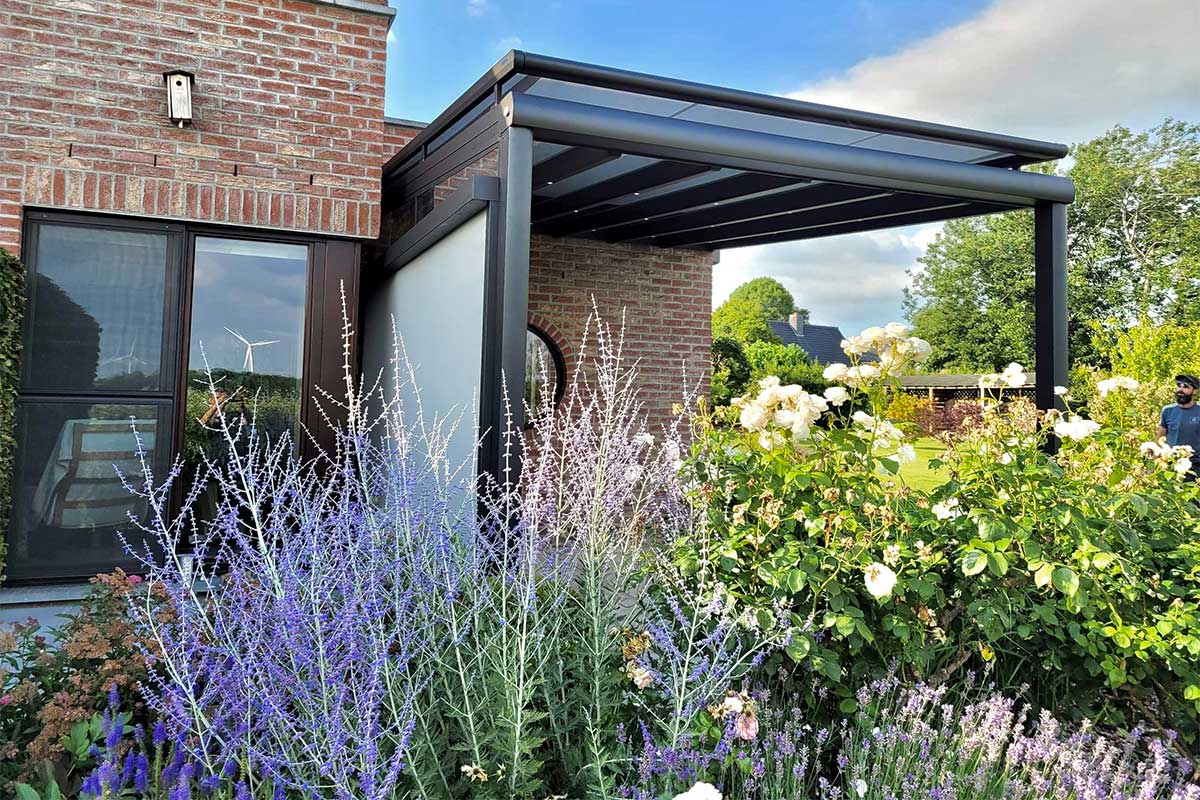
La pergola à toiture fixe
VERANDAIR®, fabrique votre pergola à toiture fixe. Cette installation offre confort et esthétisme à vos extérieurs. La pergola à toiture fixe est un véritable lieu dédié à la détente. Lorsque les beaux jours sont de retour, une pergola à toit fixe permet de profiter de la météo clémente tout en offrant une protection contre les UV, le vent et la pluie.
Unique et agréable, la pergola à toit fixe VERANDAIR® est composée de profilés en aluminium et est couverte d’une toiture transparente en verre transparent ou opaque pour une meilleure protection. En fonction de vos envies, la pergola VERANDAIR® se personnalise pour correspondre au mieux à votre habitation et à votre style.
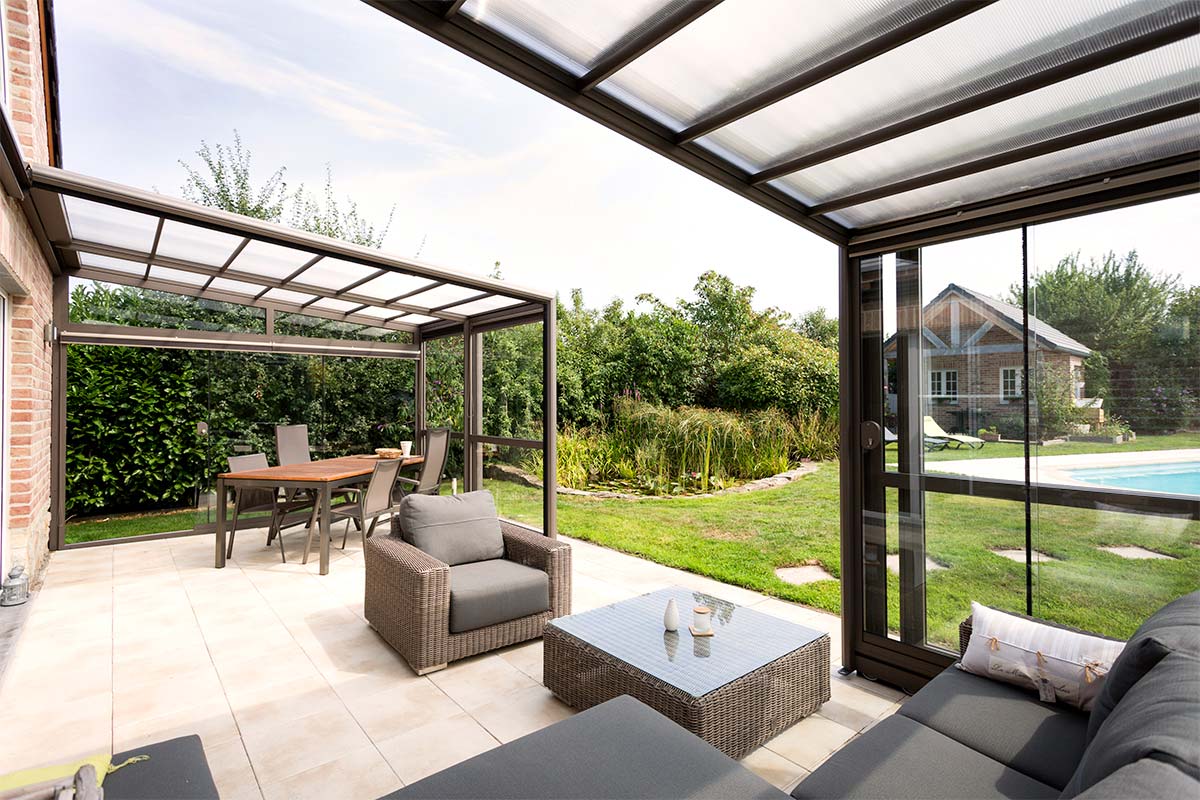
La pergola rétractable
La pergola rétractable VERANDAIR® permet d’aménager votre extérieur de façon agréable et conviviale, quelle que soit la météo.
Lors des journées plus fraîches ou pluvieuses, cette pergola peut se fermer pour vous protéger des températures hivernales, du vent et des averses. Lors des beaux jours, elle s’ouvre afin de vous faire profiter du soleil. Votre pergola rétractable s’adapte donc à toutes les saisons, afin que votre terrasse soit utilisable quand vous le souhaitez !

L’abri de terrasse
La météo souvent capricieuse ne vous permet pas de profiter de votre terrasse au maximum ? L’abri de terrasse apporte une solution esthétique et conviviale à votre extérieur.
L’abri de terrasse vous offre un espace de vie lumineux où vous pouvez profiter des extérieurs tout au long de l’année. Vous bénéficiez d’un lieu où profiter de la beauté des paysages blancs en hiver, du soleil en été ou simplement de son jardin tout en étant protégé.
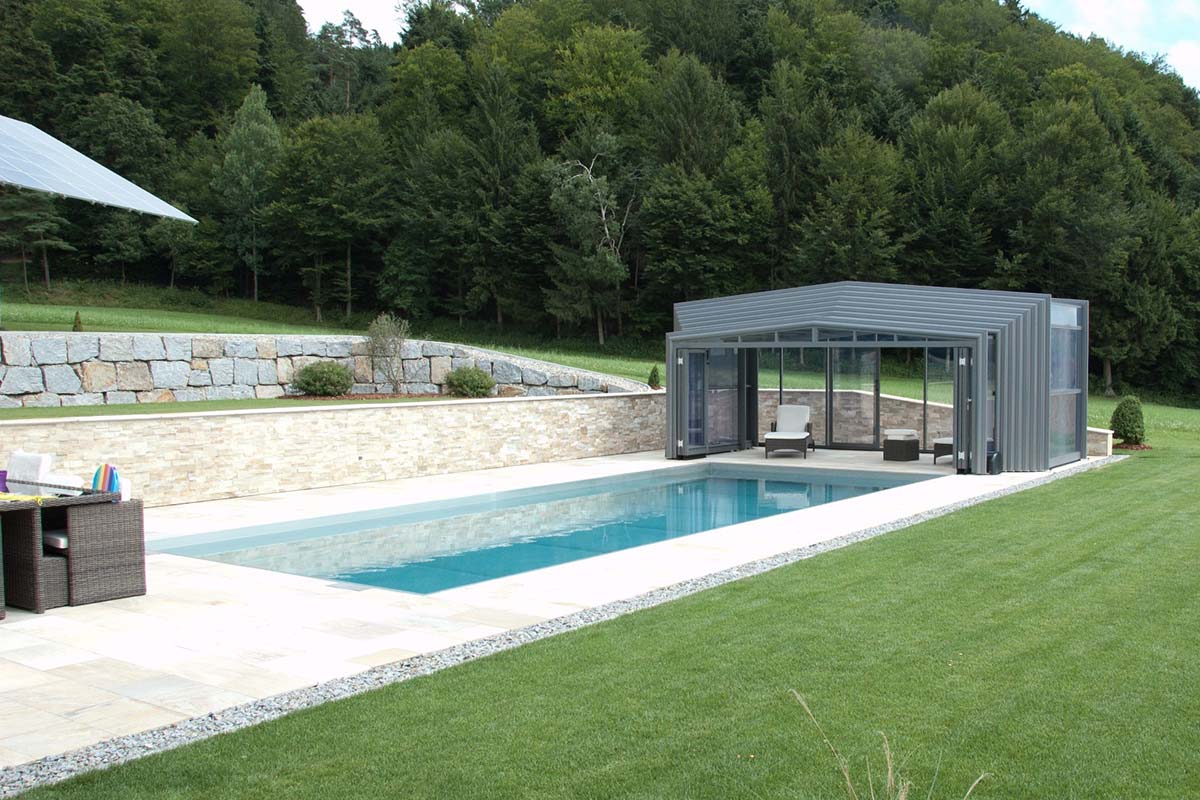
L’abri de piscine
Profitez de votre piscine à tout moment de l’année avec un abri de piscine VERANDAIR®. Cette solution pratique et esthétique vous permet de vous baigner dans votre piscine peu importe la météo.
Rétractables, les abris de piscine VERANDAIR® s’ouvrent et se ferment selon vos besoins. Fermé, l’abri de piscine vous offre une piscine couverte comme une extension, protège votre installation et conserve l’eau à une température agréable. Ouvert, il vous permet de profiter de votre piscine extérieure par beau temps.
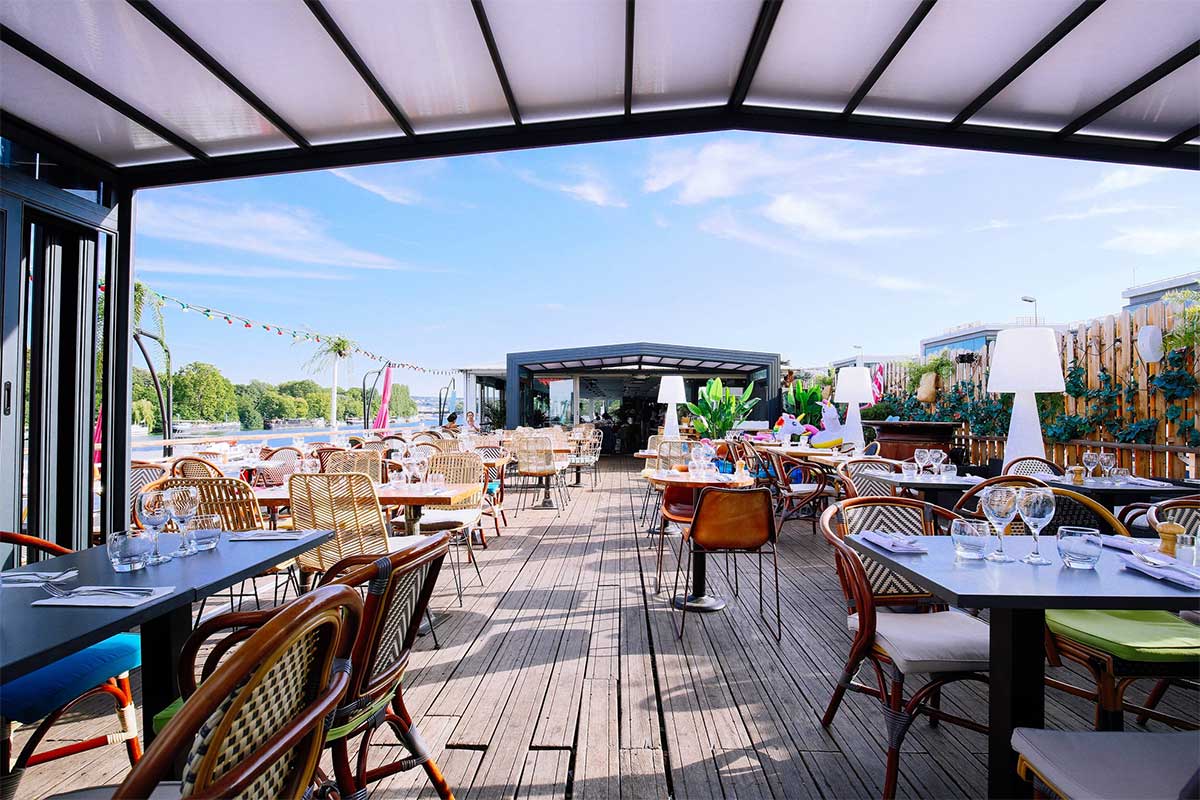
La véranda pour HORECA
Dans le secteur de l’Horeca, posséder un extérieur est un grand atout. Une terrasse dans un restaurant ou un café représente un espace agréable qui permet d’accueillir plus de clients qui peuvent également profiter du beau temps. Cependant, lorsque la pluie s’invite, il est nécessaire de replacer les clients à l’intérieur et, une fois l’hiver venu, cet extérieur devient alors inutilisable.
Une véranda pour Horeca répond à cette problématique. Elle offre un espace lumineux où les clients peuvent profiter de l’extérieur. En quelques secondes, elle se plie et se déplie au gré de la météo pour offrir la meilleure expérience à vos clients.
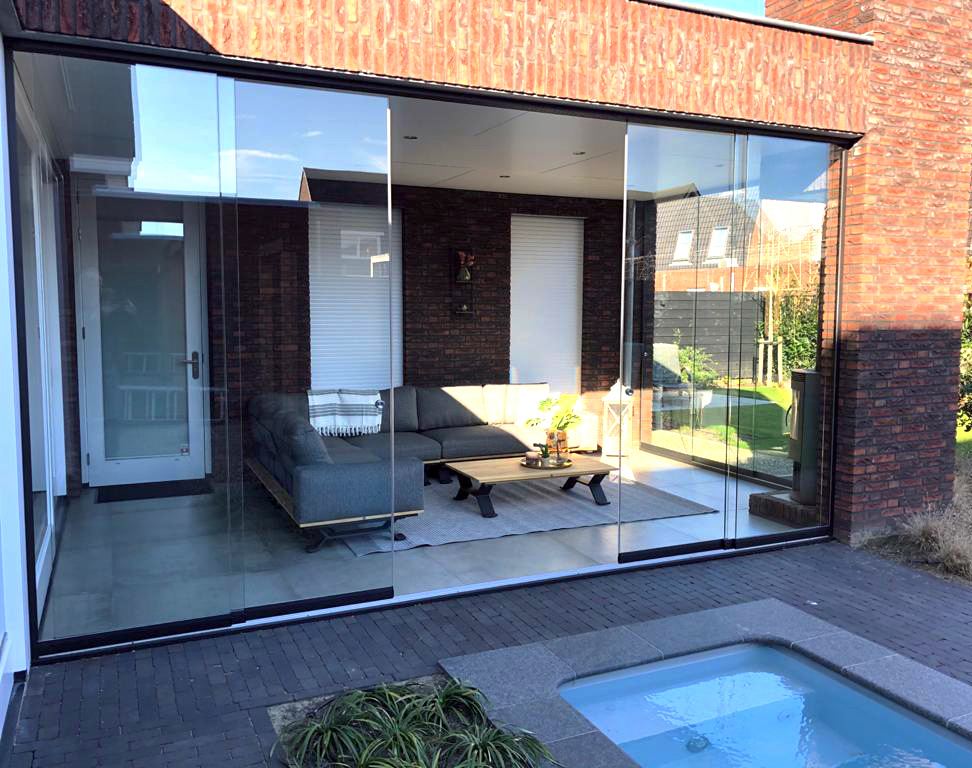
La baie vitrée coulissante
Véritable puits de lumière pour votre habitation, la baie vitrée coulissante est une solution avantageuse pour embellir votre maison et lui offrir une agréable ouverture sur vos extérieurs.
Également prévues en complément de vos constructions de pergolas à toit fixe et pergolas bioclimatiques, nos parois en verre sont aussi idéales pour protéger vos abris des intempéries. Elles peuvent être choisies en option de votre projet de construction ou ajoutées à un abri existant.
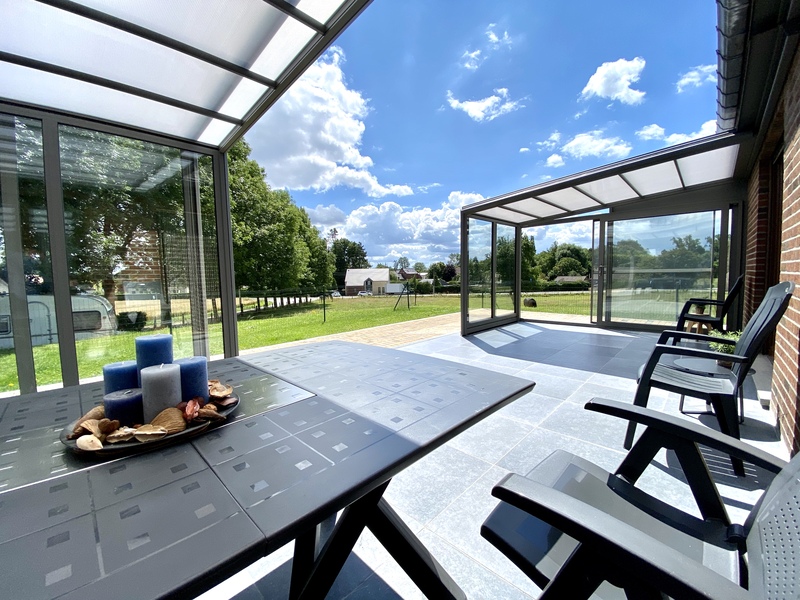
La véranda rétractable
La véranda rétractable VERANDAIR® allie les avantages d’une véranda traditionnelle et d’une terrasse couverte !
Le ciel présente un grand soleil ? En quelques secondes, ouvrez votre véranda et profitez du beau temps. Une averse arrive, pas de problème, l’installation se déploie en quelques secondes. Une facilité d’utilisation pour profiter de votre extérieur en toute circonstance !
Les avantages d’une pergola VERANDAIR®
Extension modulable
La pergola permet d’agrandir une pièce de vie comme une extension. Une pergola rétractable vous permettra de profiter de votre terrasse tout au long de l’année, mais également de créer des espaces modulables selon les saisons et vos envies. Ainsi, au fil du temps, votre pergola pourra être une terrasse couverte, un atelier, un espace de détente, un bureau à ciel ouvert… C’est à vous de décider !
Apport de luminosité
La pergola à toiture fermée, bioclimatique à lames orientables ou rétractable vous permet de profiter d’un espace extérieur tout en vous offrant de la lumière naturelle. Même si la météo n’est pas agréable, vous bénéficiez d’une plus grande luminosité.
Design moderne, personnalisé et sur mesure
Les pergolas VERANDAIR® sont fabriquées sur mesure en fonction des dimensions souhaitées. Personnalisables, elles s’adaptent parfaitement à votre maison et à vos extérieurs afin d’offrir un design moderne et élégant.
VERANDAIR® , l’expert de la pergola rétractable pour les particuliers et les professionnels
Depuis plus de 30 ans, VERANDAIR® conçoit et fabrique des pergolas rétractables en Belgique. Située à Spy, non loin de Jemeppe-sur-Sambre, en Belgique, l’entreprise VERANDAIR® est quotidiennement active dans toute l’Europe, mais également en Afrique et en Amérique du Nord.
Aujourd’hui, plus de 6.000 pergolas VERANDAIR® sont la preuve d’un travail de qualité et de passion. Un travail qui a permis à l’entreprise familiale de positionner en tant que spécialiste des structures en aluminium rétractables.
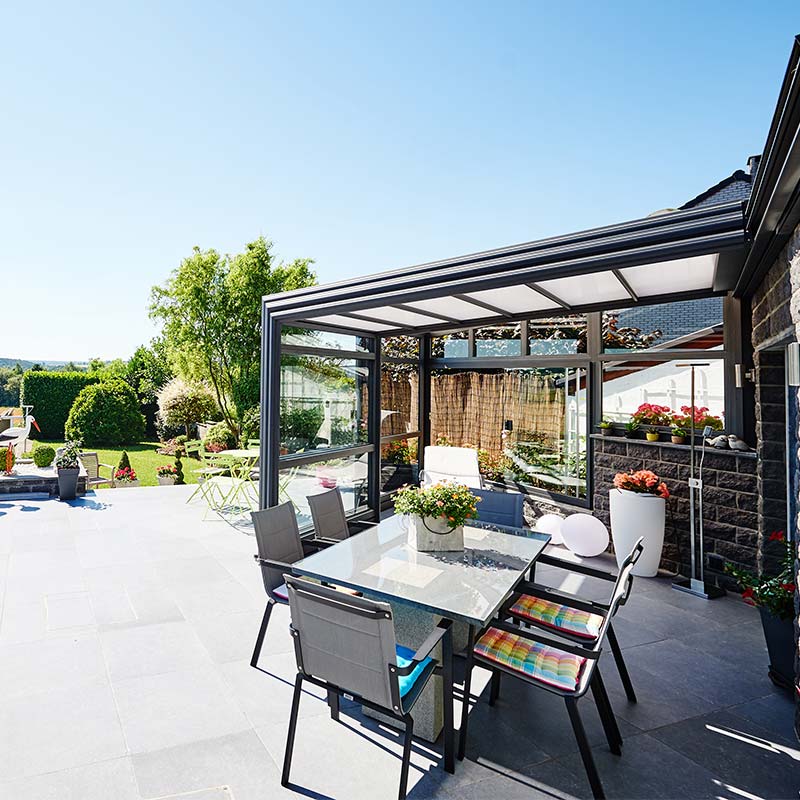
clients satisfaits
collaborateurs dévoués
années d'expérience
Nos valeurs
Qualité
Nous fabriquons nos pergolas et abris de terrasse et de piscine en Belgique, à Spy, avec des matériaux 100 % renouvelables. Nous vous proposons des structures en aluminium solides, esthétiques et durables à un prix attractif.
Intégrité
Chez VERANDAIR®, nous traitons votre projet avec intégrité, transparence et honnêteté. Nous restons fidèles à nos engagements, que ce soit au niveau de la qualité de nos produits et services ou de nos démarches écoresponsables.
Respect
Votre satisfaction est notre priorité. Nous communiquons avec clarté et écoutons attentivement vos besoins. Nous nous assurons que chaque projet corresponde à vos envies et exigences. Nous nous engageons à créer une expérience client exceptionnelle.
Disponibilité
Afin de vous fournir une expérience client de qualité, notre équipe se tient à votre disposition pour répondre à vos questions et vous proposer des conseils et solutions personnalisés. Flexibles et disponibles, nous vous proposons un service client rapide et professionnel.
Avis et témoignages
Nos clients parlent de nous
Nos actualités
Tendances, réalisations et astuces : retrouvez toutes les actualités sur la véranda, la pergola, la baie vitrée coulissante, l’abri de piscine et l’abri de terrasse sur le blog de Verandair.
Nos solutions pour protéger votre véranda de la chaleur
Découvrez toutes les solutions pour protéger votre véranda de la chaleur et profiter d’un espace frais même en plein été.
Nos conseils pour la rénovation de votre terrasse extérieure
Rénovation de terrasse : astuces pour donner un coup de jeune à votre extérieur Avec le temps, votre terrasse peut…
Comment aménager une terrasse au style jardin japonais avec une pergola ?
Transformez votre terrasse en jardin japonais zen avec une pergola. Choisissez les bons éléments de déco avec nos conseils.
Comment occulter une pergola ?
Inspirez-vous de nos conseils déco pour transformer votre pergola en un coin détente stylé, confortable et naturellement intégré.
7 idées de décoration de pergola pour sublimer votre extérieur
Inspirez-vous de nos conseils déco pour transformer votre pergola en un coin détente stylé, confortable et naturellement intégré.
5 astuces pour réussir votre pergola végétale
Envie d’un coin ombragé et fleuri ? Suivez nos 5 conseils pour créer une pergola végétale harmonieuse, robuste et accueillante.
Comment fonctionne l’évacuation de l’eau dans votre pergola ?
Découvrez les meilleures solutions d'évacuation d'eau pour préserver la durabilité de votre pergola et profiter pleinement de votre espace extérieur.
Comment optimiser l’ombre sous votre pergola ?
Découvrez des astuces pour aménager un ombrage parfait sous votre pergola et profiter de votre extérieur toute l'année.
Pergola contre la pluie : comment protéger votre espace extérieur ?
Optimisez votre terrasse avec une pergola qui vous protège de la pluie. Choisissez entre modèles rétractables ou traditionnels.
Installer votre pergola en zone venteuse : quelles solutions pour résister au vent ?
Pergola en zone venteuse ? Optez pour une installation robuste avec nos conseils pour résister aux rafales et sécuriser votre…